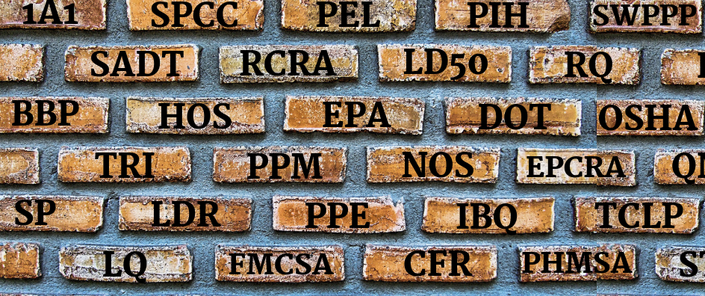
The Survival Guide for New EHS Managers
How to Master your EHS responsibilities even if you’ve never done it before
Get started now!
The Survival Guide for New EHS Managers
How to handle your EHS responsibilities
even if you’ve never done it before
What You Don’t Know Can Hurt You
Have you ever been blindsided by something unexpected?
Like that flat tire on the side of the highway, or that embarrassing sound when your card has been declined at the checkout counter?
Well, it can get a lot worse than that.
Imagine that you just found out the hard way that:
- OSHA, EPA and DOT fines had increased by 80% a few years ago, and your boss is livid after receiving a fine of $50,000 for a couple minor violations,
- Or that your OSHA 300 Logs had to be reported electronically for the last 3 years, and you didn’t know,
- Or that EPA had completely revamped all the hazardous waste management rules, but you didn’t get the memo,
- Or that the DOT rules for Lithium Battery packaging had changed yet again and a rush shipment to your best customer is being returned by the carrier.
Now what are you going to do?
Don’t Leave the Company Vulnerable
All too often, the Environmental, Health and Safety (EHS) duties are assigned to someone who has little knowledge of the rules and even less time to implement them. This leaves their company vulnerable to big problems.
To make things worse, the regulations are changing every year. If you have not updated your company's EHS programs in the last few years,then you are falling behind.
The employee safety, waste management, and Hazmat compliance functions at your company must be managed by someone who knows what they're doing. Too often though, EHS duties are viewed more like a punishment, and not as a critical business function.
Program Failure often results from scenarios like these:
- You’re the new guy at work, and all the dreaded EHS duties are handed to you like so many hot potatoes
- You’ve been the EHS manager for a while and figured that everything was OK, so you just left it on auto-pilot, for years
- You've inherited the EHS role and just assumed that the waste and safety programs were all settled by the person before you
- Company management have discovered that there really are rules governing one or more of their operations and you have been chosen to get everything fixed, despite your complete lack of experience
- Your supervisor saw an article about a competitor who got fined hundred of thousands of dollars for running a piece of equipment just like you do, and the HR person is crowned as the Safety Manager too
- The president of the company watched a video of a company that burned to the ground for mishandling the same kind of chemicals you use, and the Maintenance Supervisor is told to prevent it from happening here
- The company was fined for some violations, and the Production Manager been given the task of getting everything straightened out, pronto
- You’re the new Branch Manager and you know that compliance has gone down the tubes, but your first priority is monthly quotas, and EHS is permanently put on the back burner
Unless you have a knowledgeable person watching over your EHS programs, you have a weak spot that leaves you open to serious problems.
Sadly, most of the thousands of businesses I have seen over the last 35 years have assigned this vital task to people who don’t have the knowledge they need. It appears that everything is doing well, until something hits the fan and all hell breaks loose.
I have personally seen a company make ONE mistake, and it cost them everything.
Equipping Your EHS Manager
How, then, can you prevent compliance failure and protect your company from the cascading costs that usually result from a regulatory meltdown …?
… By giving your EHS person the right tools.
When I created the Survival Guide for New EHS Managers, I wanted to lay out a detailed map of how you can get started.
I took a Big Picture approach, assembling a plan that enables you to gather all the information you need to connect the dots between operations and regulations.
The Survival Guide is designed for people who are new to the wonderful world of OSHA, EPA and DOT regulations.
The Survival Guide will take you rapidly from;
- An initial evaluation of the facility operations and materials,
- To assessment of workplace hazards,
- To determination of applicable regulations,
- Then to identification of regulatory requirements,
- And finally to compliance with the rules you are subject to.
That is the overall objective of the course: To help your EHS Manager develop the programs that will fulfill your legal duties as an employer.
Fear of the Regulations
I have a short story that demonstrates one reason why I have spent close to 150 hours creating the Survival Guide for New EHS Managers.
On a windy New Mexico afternoon, a shopping cart blew into my car and dented the door. I brought the car to a local body shop and the owner came out to see the damage. We agreed on a price for the minor repair.
As we walked back to the office, he casually asked what I did for a living. I told him that I help the hyper-regulated business owners and managers of America cope with the burdens of the OSHA, EPA and DOT regulations.
He stopped and turned towards me with the most serious look you can imagine, and said these words: “The thing I fear the most, is OSHA walking in that door.”
That statement absolutely floored me. It's almost inconceivable that a small business owner would be more afraid of OSHA than bringing in enough revenue to keep the lights on, or anything else.
Why, though, was Mr. Sanchez so afraid? Simply put, he was scared crapless because he had no idea what OSHA was all about. It was his lack of knowledge about the OSHA regulations that gave him such great fear.
The really sad part is that he’s not the only one.
And that is why I created the Survival Guide for New EHS Managers, and several other courses, services, and programs – Because you shouldn't have to live in fear of OSHA too.
What Would Happen If ...
So, now that you know what the course is all about, it’s time to decide to buy it, but first, I propose a little thought experiment for you;
Just imagine, it’s Monday morning and you’ve been at work for an hour or so. You’re sitting at your desk and you’ve hit your stride. Things are going smoothly, and you are knocking the heck out of that big project you had put off all last week. It looks like it’s going to be a pretty good day.
The intercom beeps and it’s that pretty young gal in the reception area you’ve had your eyes on.
“OSHA is here to see you”, she says.
What happened when you read those words?
Did the pit of your stomach drop into your shoes? Did your pulse instantly double? Did a cold sweat break out down your spine?
My recommendation is this: If you had any of those reactions, then you know you’re not ready. You know those inspectors would eat you for lunch. You know it would be ugly.
Why wait until they “…walk in that door”? Take the Survival Guide for New EHS Managers. Take the initiative to get your EHS compliance in order.
Curriculum for the Survival Guide
But first, here is an outline of the 12 Lessons in the Survival Guide:
Lesson 1 – Introduction: An over view of the course and a discussion of the common malady I call “New EHS Manager’s Syndrome”
Lesson 2 – You’ve Been Selected: How and why your were chosen to ensure regulatory compliance for your company. What Environmental, Health and Safety is all about.
Lesson 3 – Taking the Reigns: Find out what your boss wants and how you will deliver the goods.
Lesson 4 – Your EHS History: How to find existing EHS records. The Big 3 Regulations, OSHA, EPA and DOT.Determining the chain of command.
Lesson 5 – Your Compliance History: How to find the relevant permits, registrations, and ID numbers that are so important to compliance. Taking your first casual walk around the facility.
Lesson 6 – Fact-Finding Mission #1: Taking your second look around and finding the key personnel in the operational areas. Asking questions and taking notes.
Lesson 7 – Regulatory Issues: Matching operations to the regulations. Taking a deeper look into the EPA, DOT and OSHA regulations.
Lesson 8 – Analysis: Identifying and listing the regulatory implications for each of the operations.
Lesson 9 – Summary of Findings: Summarizing the information for presentation to the boss. Producing a 30/60/90 day plan.
Lesson 10 – Conclusion: Prioritizing any programmatic deficiencies and determining the actions needed to get into compliance.
Lesson 11 – Potential Difficulties: Taking this task seriously and some of the problems that can occur if the problems aren’t fixed.
Lesson 12 – Expectations: How we will use accountability to make sure you finish the course and apply the information.
And I almost forgot to tell you about my 30 day, unconditional, money-back guarantee …
... and the supporting documents, links and resources that will enable even the most inexperienced beginner to get off to a quick start
… and the Private LinkedIn Group you will be invited to, where you can ask questions and have access to our live calls.
But most of all, you’re going to get some peace of mind, and some confidence that you finally have taken a positive step in the direction of EHS Happiness.
Lastly, if you have any questions, you can reach me by phone or mail:
Ron Harvey
(843) 599-0330 – Mountain Time
SHOW THIS TO YOUR BOSS.
I know that some of my students will have to get permission to purchase this course.
You can take or send the document below to your boss and it will give a full description of the course contents.
If you have to take this route, please make sure that that the enrollment is done with your name and your email address.
Go to this link to get the form: SHOW THIS TO YOUR BOSS.
Here is the full URL - https://drive.google.com/file/d/1XsTMSRsHfn9FWpCNdDv4l2Rg8XicTKe6/view
Your Instructor
Business owners start companies to make money, not to become Environmental, Health and Safety (EHS) experts.
I’ve learned a few things about compliance during my 34 years in the hazardous waste business and I’ve seen the best and the worst compliance situations.
This is often the scenario: The person in charge of safety & environmental programs has 1 or 2 other hats to wear, and the EHS hat never seems to end up on top. The result is that compliance gets neglected - until the sh*t hits the fan.
EPA, DOT and OSHA rules are complex and confusing, and they apply to multitudes of organizations of every size in every sector of the economy. After seeing the insides of thousands of businesses, I estimate that 50% at best are in significant compliance. The rest are doing what I call “seat of the pants compliance”; just doing the bare minimum and hoping nothing bad happens.
Don't be like them.
I believe that you've read this far because you are concerned for worker safety and environmental protection at your company. My recommendation is that you enroll in this course because you are the kind of manager I like helping the most - You want to do the right thing, but you just haven't figured out where to begin.
Compliance actually is very simple, if you have someone to show you the way.
Course Curriculum
-
StartStart Here (1:40)
-
StartLesson 1 - Introduction (7:29)
-
StartLesson 2 - You've Been Selected (10:15)
-
StartLesson 3 - Taking the Reigns (8:42)
-
StartLesson 4 - Your EHS History (14:04)
-
StartLesson 5 - Your Compliance History (11:47)
-
StartLesson 6 - Fact-Finding Mission #1 (10:02)
-
StartLesson 7 - Regulatory Issues (14:55)
-
StartLesson 8 - Analysis (8:10)
-
StartLesson 9 - Summary of Findings (14:36)
-
StartLesson 10 - Conclusion (8:23)
-
StartLesson 11 - Potential Difficulties (17:46)
-
StartLesson 12 - Expectations: It's Your Move